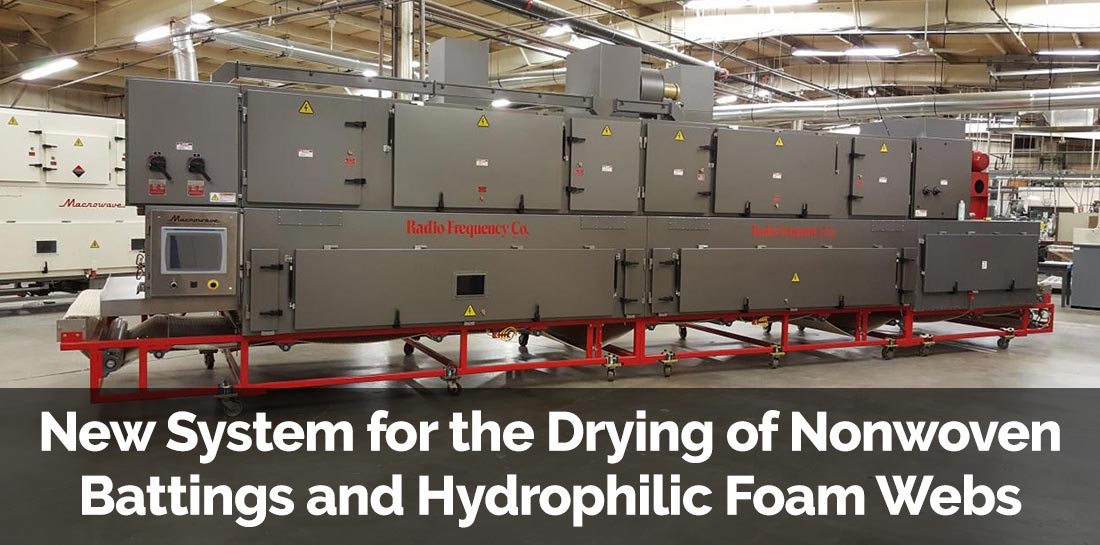
02 Oct Radio Frequency Company (RFC) Introduces a New System
Radio Frequency Company Introduces a New System for the Drying of Nonwoven Battings and Hydrophilic Foam Webs
The drying of nonwoven battings and foam webs have always presented challenges for conventional dryers due to their thermally insulative properties. Generally, this leads to prolonged drying times and non-uniform moisture content of finished products. Energy efficiency is low as a result of this drying challenge and often times, greenhouse carbon emissions are high. Because of the unique characteristics of radio frequency heating, these products can now be dried with excellent efficiencies and require a fraction of the factory floor space.
In a radio frequency dryer, product is conveyed between two high frequency electrodes which cause the polar water molecules within them to constantly reorient themselves to face the opposite poles. This molecular action creates friction which quickly turns the water into a gas, insitu, where it then can be efficiently removed. Because the water exists the batting or foam as a gas, particulates such as binder materials or antimicrobials do not to migrate to the surface as is seen with conventional dryers which rely on capillary action in the drying process.
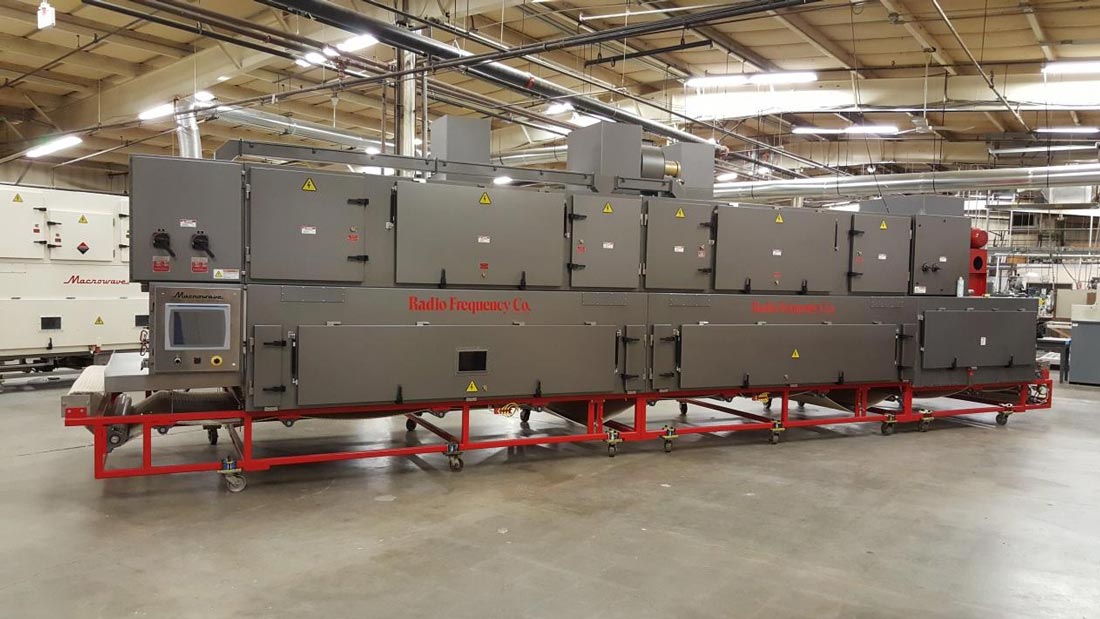
New 240kW Nonwoven Batting Dryer with Vacuum Assisted Curing Zone
These new dryers are employed both as a means to handle 100 percent of the drying requirement, and also in a hybrid manner to dry only the remaining internal moisture after the thermal efficiencies decline during a conventional drying process. As a hybrid dryer on an existing line, increases in line productivity often increase by 50 percent or more. For thermally sensitive materials, productivity gains are greater as the RF drying process does not create temperatures higher than the boiling point of water.
Radio Frequency Company was founded in 1946 and is the world’s largest producer of RF heating systems. New systems are available in a complete range of sizes to match a client’s production requirements. RFC has a complete RF testing laboratory in its Millis, MA production facility for process development and also offers world-wide customer support and service on a 24/7 basis. All systems carry the UL label and are FCC and CE Compliant.
Sorry, the comment form is closed at this time.